The OKOSCAN 73HS system of combined rail testing is designed for:
- ultrasonic (UT) and eddy-current (ECT) testing of railway track at a speed up to 40 km/h and detection of all the defects specified in the UIC 712 R (International Union of Railways Code of Rail Defects);
- measurement of defect parameters and saving the testing results in the database.
The OKOSCAN 73HS system includes:
- Railroad wheeled trolley equipped with positioning system and track width adjustment control;
- Tilt adjustment control and immersion transducer units positioning system;
- Lifting/lowering mechanism for eddy-current probes;
- Ultrasonic rail test unit;
- Eddy-current rail test unit;
- Auxiliary equipment (a tank for coupling fluid equipped with a pump, level meters, pipelines and valves, air compressor);
- Hardware and software complex computer system;
- Complete kits of manual ultrasonic and eddy-current testing equipment for rails;
- Spare parts supply package;
- Technical documentation.
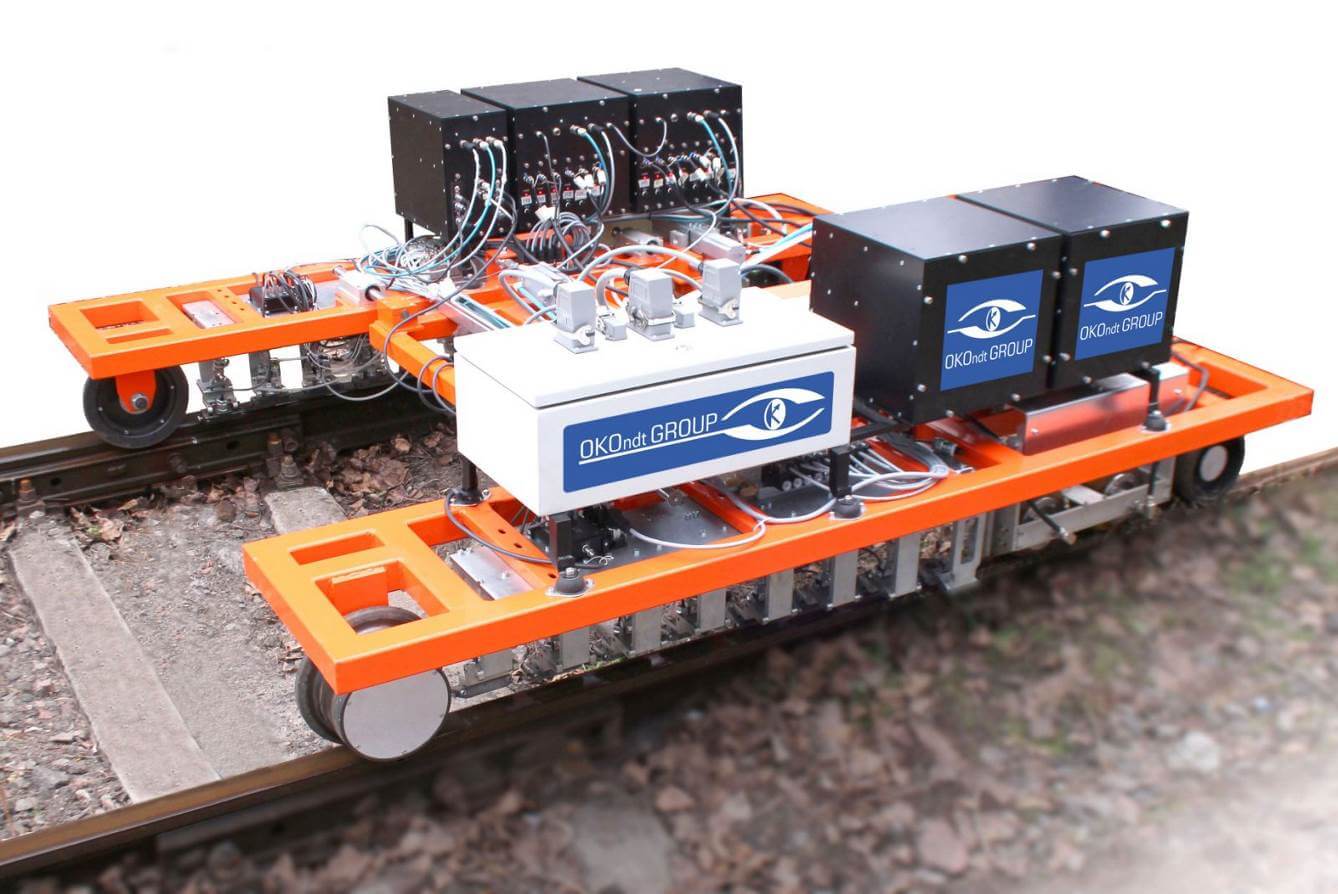
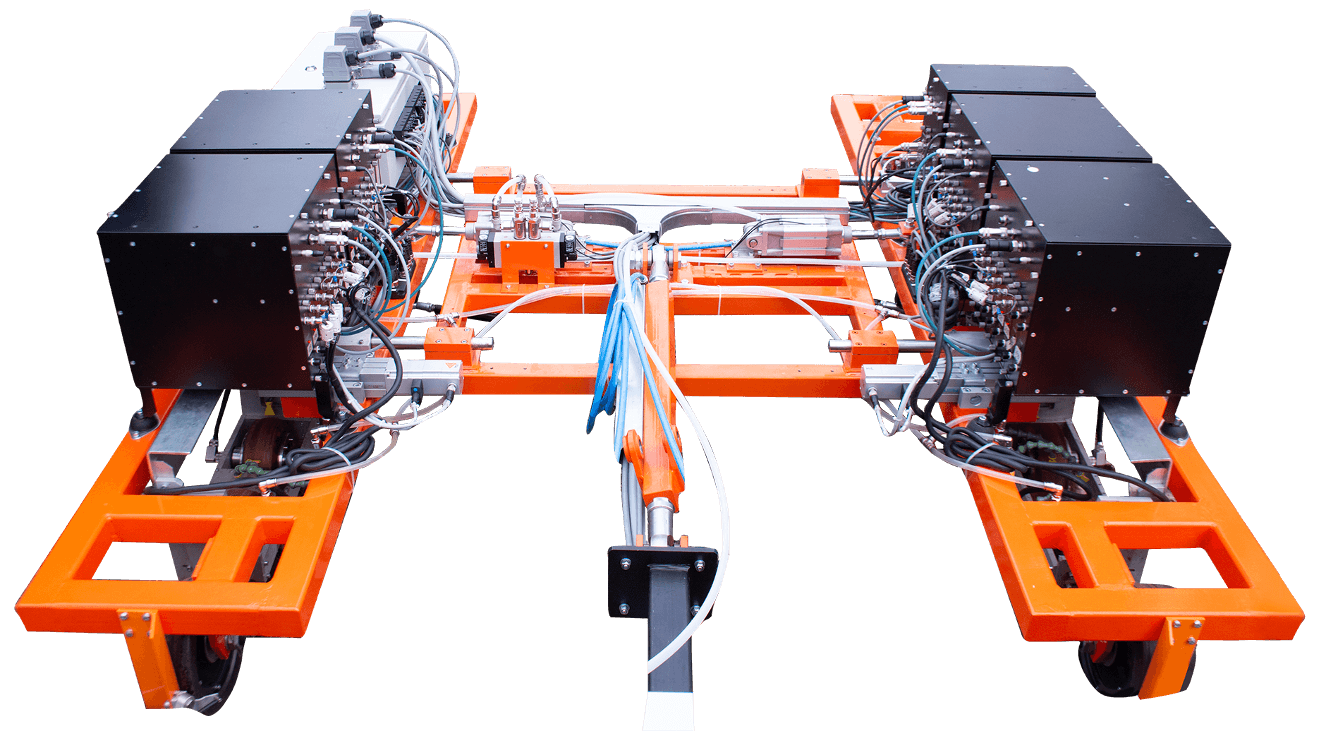
Flaw detection trolley
The trolley is a support steel structure with wheels, alignment system (pneumatics), trolley lifting and lowering mechanism (electric monorail hoist), positioning system of ultrasonic and eddy-current transducers, and water supply system for transducers immersion units.
The flaw detection trolley provides precise positioning and movement of ultrasonic and eddy current transducers (probes). Pneumatic equipment mounted on the trolley is used for automatic adjustment of the trolley to the track width. Also, this equipment allows to ensure positioning of each transducer on its own tested area.
Main advantages of the trolley:
- capabilities of testing the curves with a radius of less than 200 meters;
- automatic positioning and alignment on the track;
- ease of maintenance;
- capability of controlling the suspension system.
Ultrasonic rail test unit
Eddy current rail test unit
The eddy-current test unit consists of:
- eddy-current probes - 16 pcs;
- switches - 2 pcs;
- Eddycon D eddy-current flaw detectors - 2 pcs;
- track gauge (traveled distance sensor) - 1 pc;
- PC with preinstalled software - 1 set.
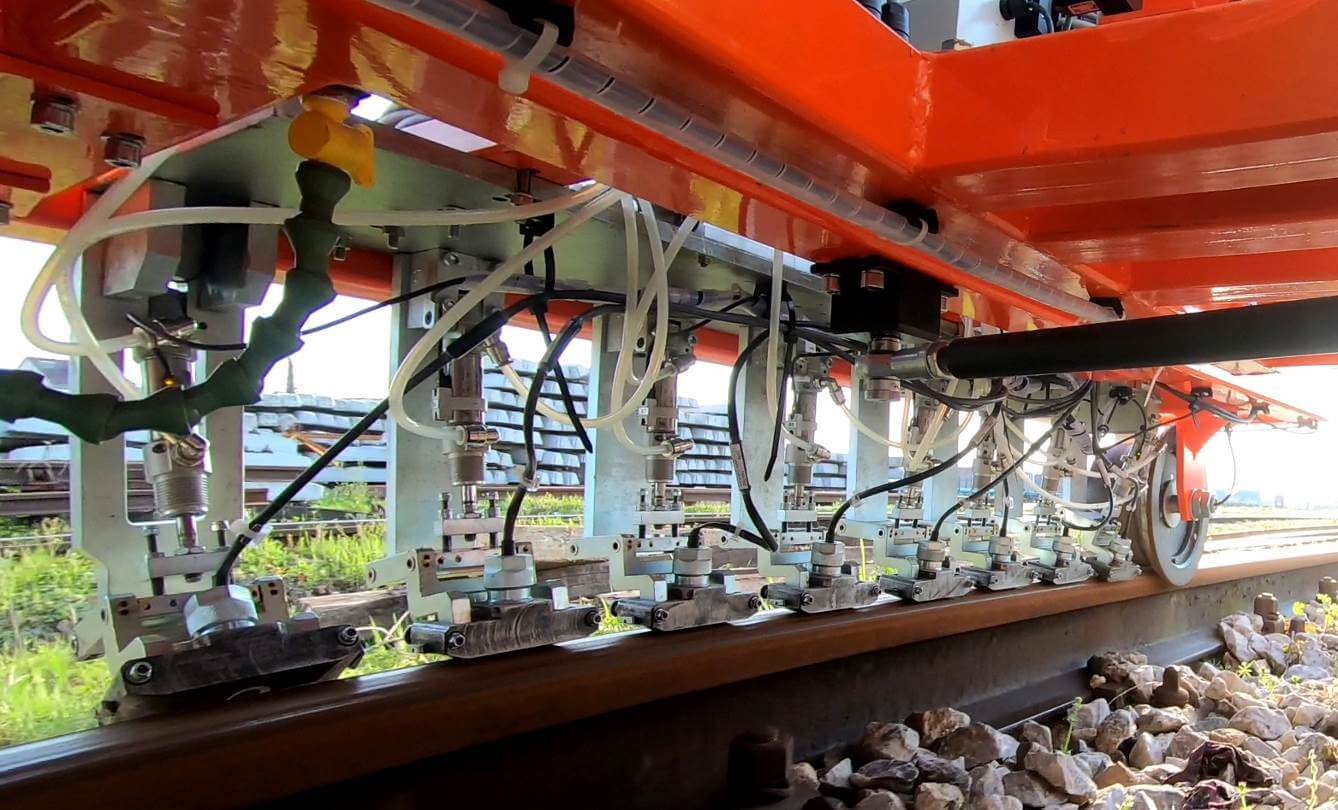
The eddy-current unit of the system provides for eddy-current examination of the working surface of the rail head and of the rail edge for the following types of flaws (defects):
- transverse fatigue cracks and headchecks (defect code UIC-211),
- quench cracks (defect code UIC-2223),
- wheel burn (defect code UIC-2251, UIC-2252),
- active face delamination (defect code UIC-2222).
Eddy Current Probes
High-speed eddy current system for rails testing OKOSCAN ET 73HS is equipped with sixteen eddy-current (probes) (ECP) - eight for each rail.
Features and technical specifications of ECT used in the system:
- the central operating frequency is 200 kHz,
- orientation of the detected defects - transverse, at an angle relatively to the rail axis,
- use of fixing bogies made of wear-resistant material,
- individual suspension bracket for each bogie to unambiguously position the probes on various rail profiles,
- clearance between the working surface of ECP and the rail surface to prevent mechanical damage of the probes.
All the ECTs are positioned on the rails so that 100% testing of the working edge and the running surface is ensured.
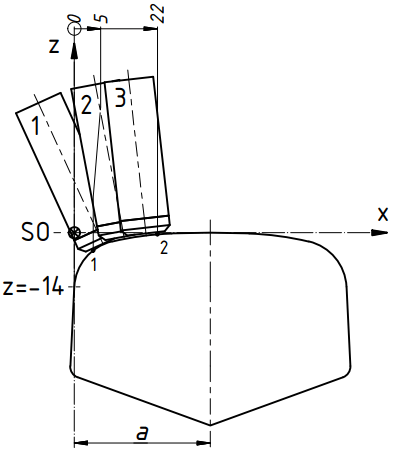
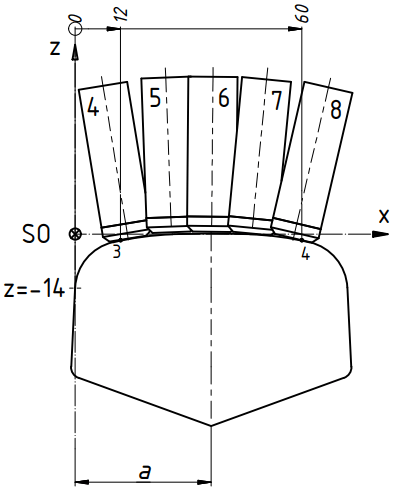
Eddy Current Flaw Detectors
High-speed eddy current system for rails testing OKOSCAN ET 73HS is equipped with two multi-channel eddy-current flaw detectors Eddycon D.
Characteristics and advantages of Eddycon D flaw detectors.
OKOSCAN ET 73HS design provides for the capability to install the flaw detectors both on the flaw detector trolley and in the cab of the rail road vehicle.
Specialized Software
For ultrasonic testing
Ref. Ultrasonic modification of OKOSCAN 73HS
For eddy-current testing
High-speed eddy current system for rails testing OKOSCAN ET 73HS is supplied with pre-installed software that consists of:
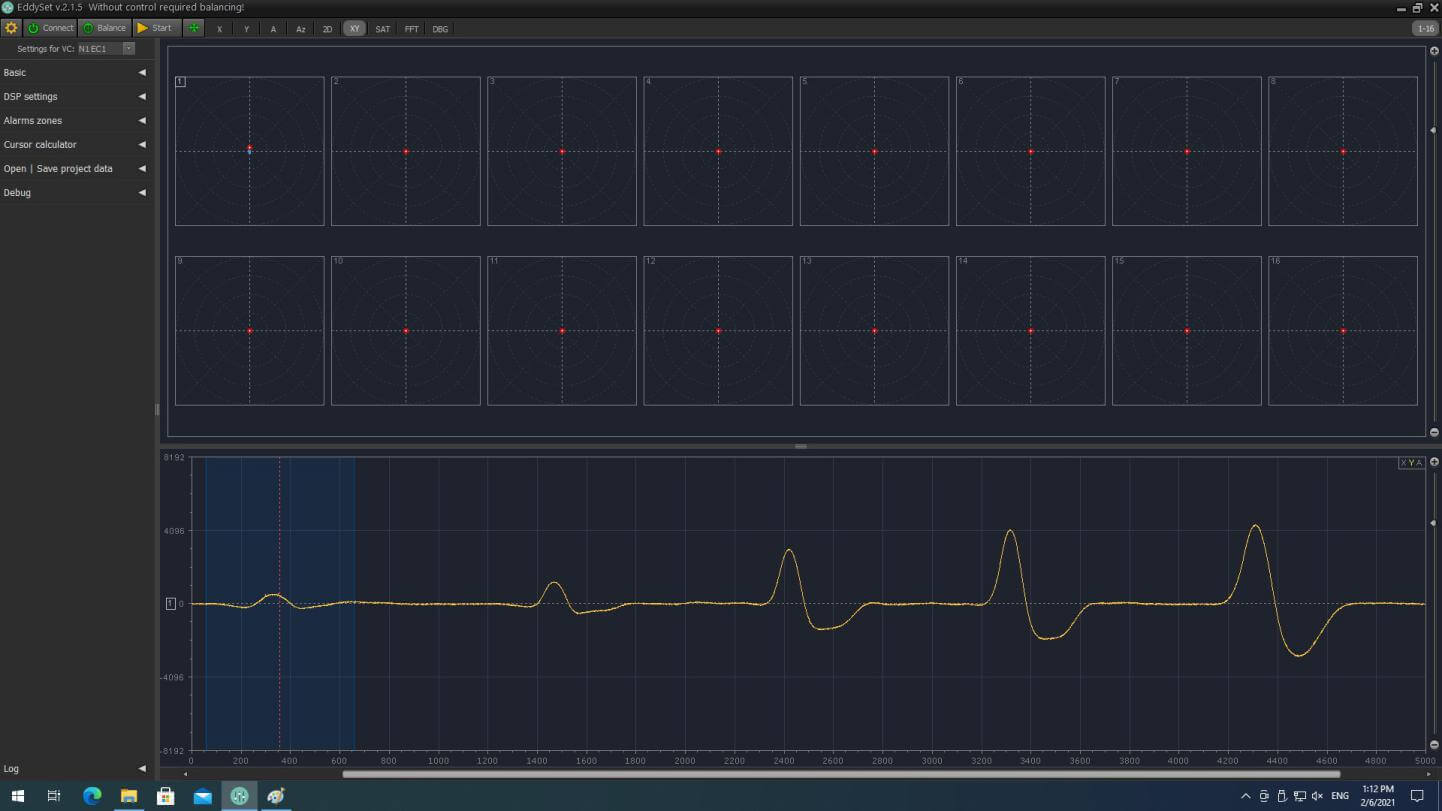
Software for setting up the flaw detectors
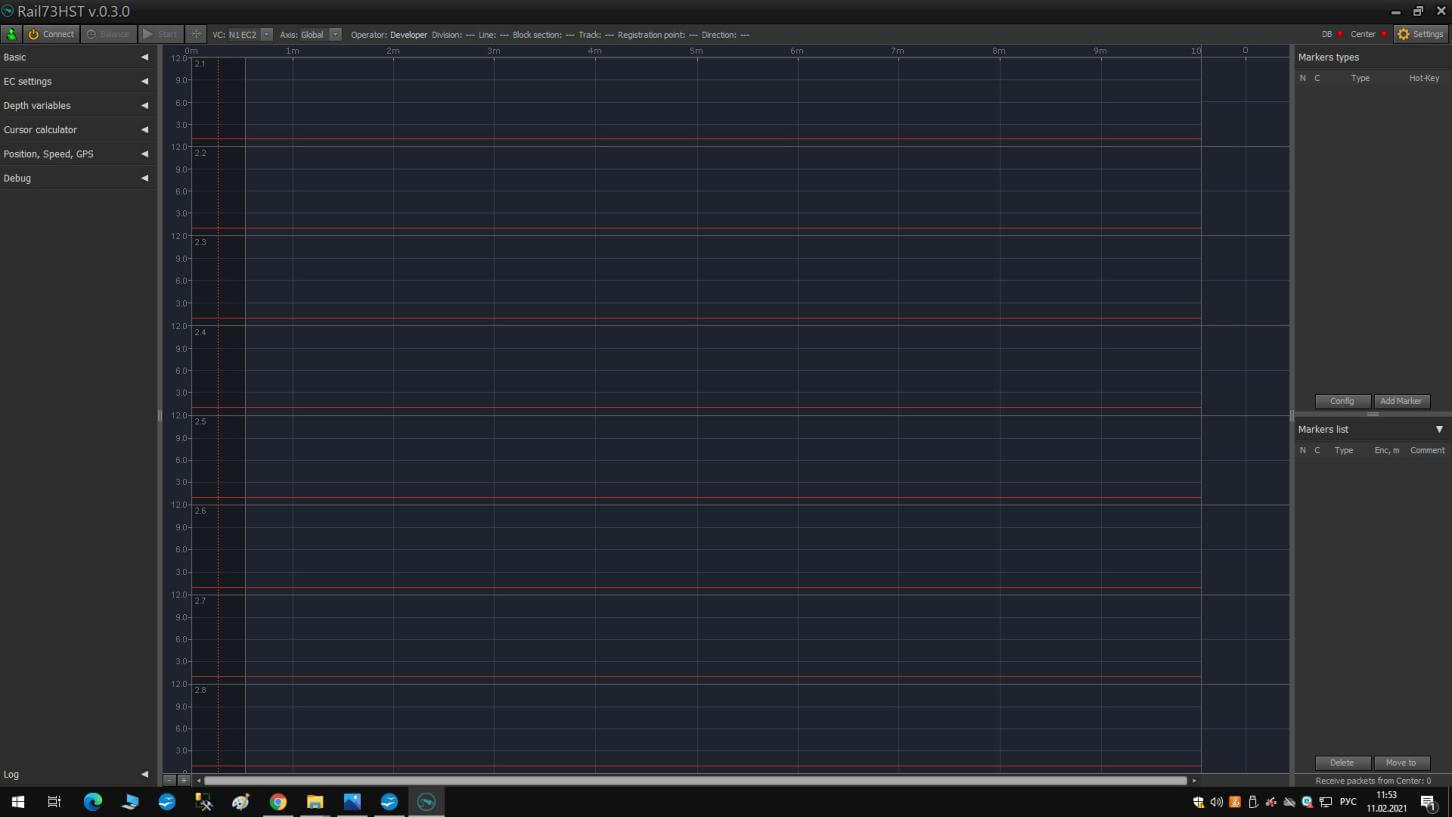
Software for control and analysis of the current data
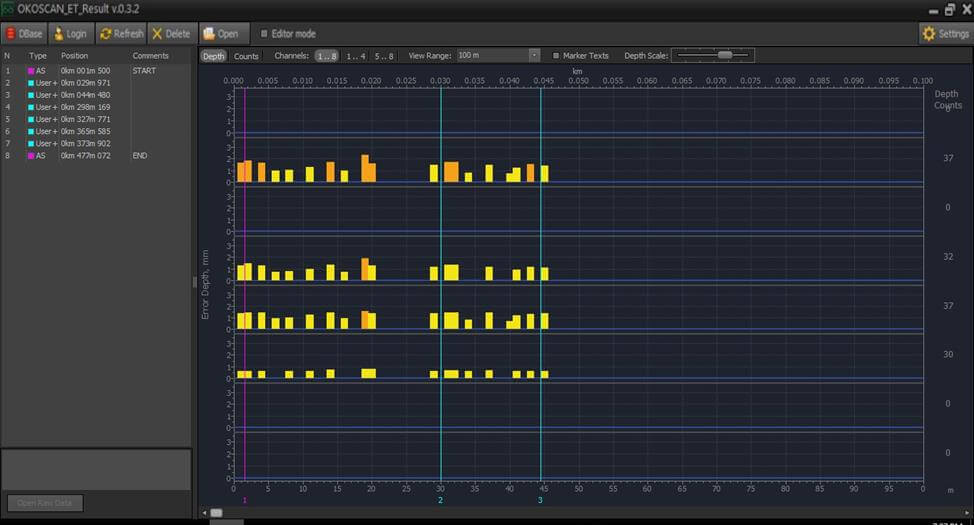
Software for viewing the testing results
Main technical specifications of the system
Product model | OKOSCAN 73 HS |
Flaw detector type | Double rail |
Areas of testing |
|
Quantity of ECPs of the flaw detector | 16 |
Quantity of ECPs per rail | 8 |
Area of coverage of the probe | 6 mm |
Probe operating frequency | 200 kHz |
ECP protection from mechanical damage and wear | Ceramic protector |
Testing speed | Up to 40 km/h |
Assessment of the cracks vertical component depth (for 25⁰ angle of the crack progression) | From 0.7 mm to 3.4 mm |
Eddy current channel | Eddycon D |
Specialized software | - Setting program - Testing program - Results viewing program |
Data record and storage | PC’s hard drive |
Operating PC | Laptop – for setting and testing programs Desktop – for results viewing program |
Detection efficiency parameters
Parameters of tested areas and of the flaws detection efficiency
Item No. | Name | Value |
---|---|---|
1 | Close dead area | Crystal probe 0° : 8 mm; Crystal probe 40° : 5 mm); Crystal probe 70° : 3 mm; Crystal probe (CCP) 55° - 5 mm; ECP - none. |
2 | Tested Area | Ultrasonic testing: Crystal probe 0° : full rail height; Crystal probe 40° : full rail height; Crystal probe 70° : rail head Crystal probe 55° - rail head; Eddy Current Inspection: 5 ECP - rail running surface; 3 ECP - rail working edge; |
3 | Resolution with references to the coordinates - Longitudinal coordinate - Depth - Rail height; | 1.0 mm; 0.1 mm; 0.1 mm |
4 | Assessment of the cracks vertical component depth by eddy- current method | from 0.7 mm to 3 mm |
5 | Accuracy of determining the parameters during ultrasonic testing: - Depth - Rail height; | ± 0.5 mm ± 0.5 mm |
6 | GPS | Recording the global positioning coordinate in the control file and then viewing it on a computer |
7 | Minimally detectable defects | Ultrasonic testing (at a 2 mm sonic test pitch) Cylindrical hole of 2 mm diameter in the rail head 5 mm deep and 1.5 mm wide groove in the working edge of the rail head (or 5 mm diameter flat bottom hole in the working edge), transverse crack simulation. 5 mm deep, 2 mm wide groove in the rail base, corrosion simulation Eddy Current Inspection: 1.2 mm deep “cut” is made on the running surface in the sectional plane |