System of Non-destructive Work rolls Testing B-35
Work rolls is the main tool of the rolling manufacture, which ensures due quality of the finished rolled products. Uninterrupted operation of the powerful rolling mill and high-quality finished products depend a lot on the mill rolls surface condition and their quality.
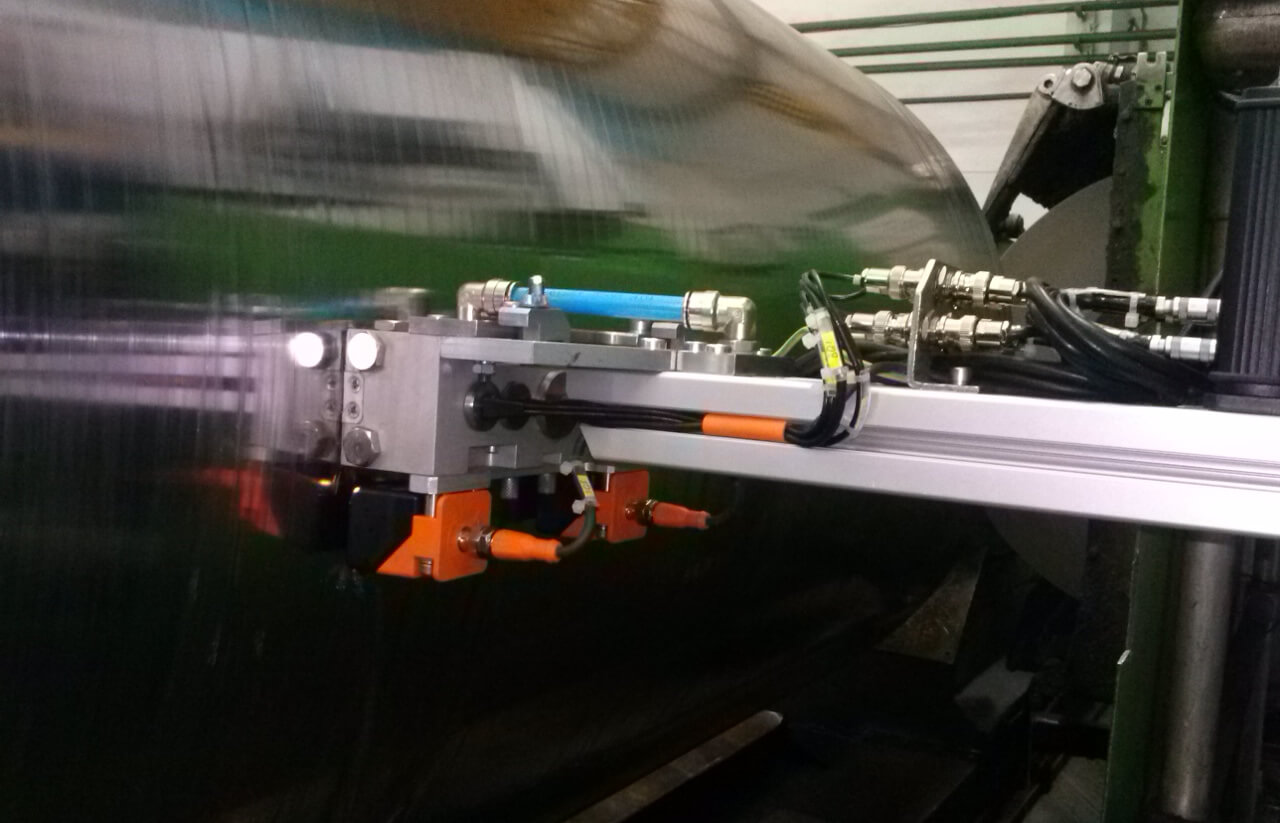
Taking into account the high cost of mill rolls, there is a need to acquire 100% of its resource, i.e. to achieve the full performance at a maximum operating cycle. To achieve the largest operating cycle of the forming rolls, the preset parameters of its repair shall be determined, e.g. in case of the net shaped roll marks or surface chips elimination, it is necessary to remove a layer having the said defect around the roll body perimeter, and in the same time not to damage the “flawless layer”. It is also required to properly evaluate current condition of a forming roll during its repair.
In order to take a correct and adequate decision regarding the surface and the roll body condition, a complex of eddy current and ultrasonic System of Non-destructive Testing B-35 is used. The system is applied as the integrated equipment for the roll-grinding machine or the lathe saddle in the automatic mode during the technological stage of the mechanical treatment. The System detects and evaluates, according to the preset parameters, both internal and surface defects of the roll body, such as metal discontinuity like reed, slag inclusion, crack, lap, сleavage, net shaped roll marks, chips and so on; it also generates the protocols of the system validity and saves the test results.
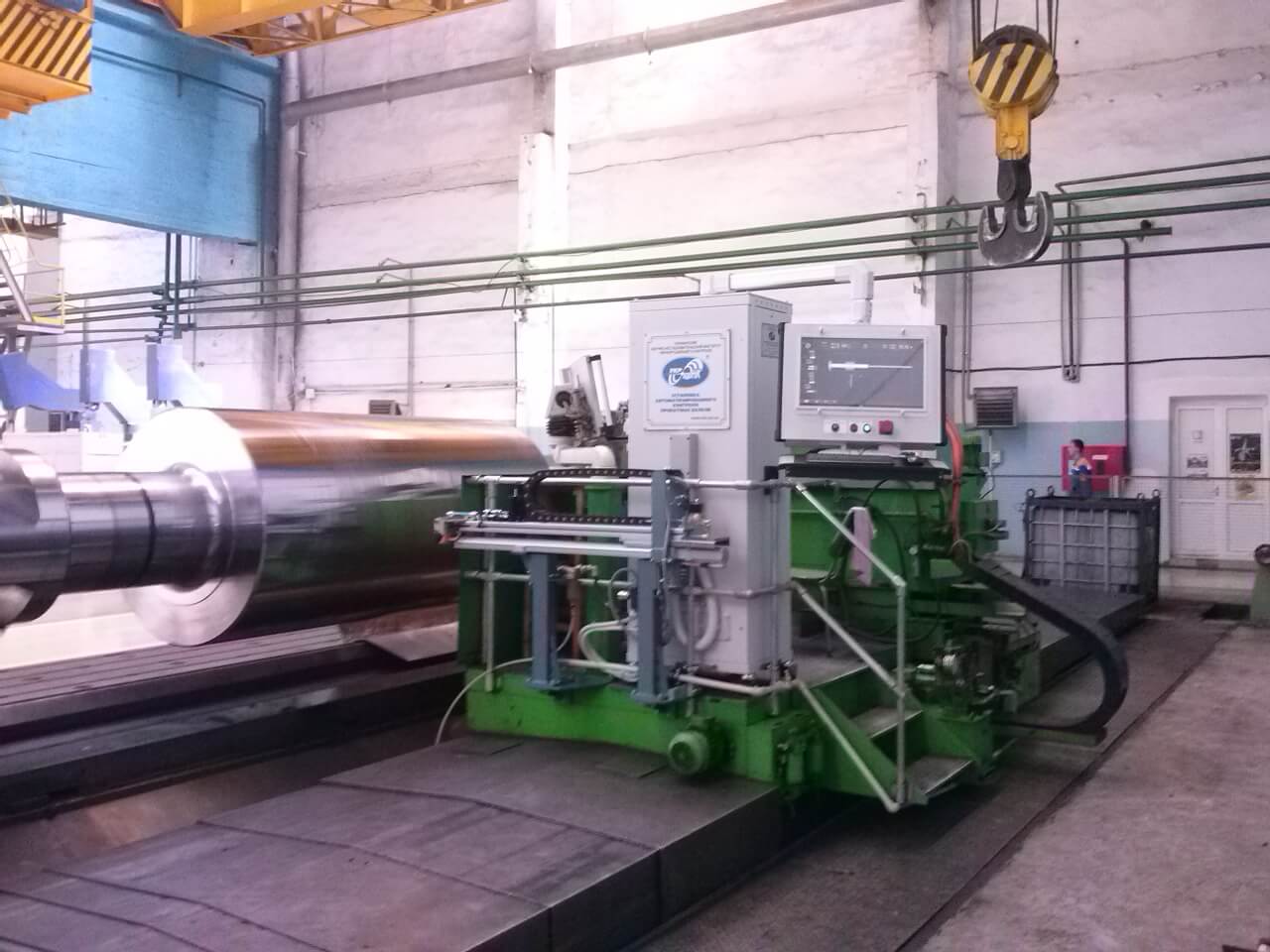
The forming rolls inspection is split by the System into three test areas, which are scanned simultaneously in one pass:
- From 0 to 3 mm depth of the forming roll scanning – eddy current test method is applied.
- From 2 to 200 mm depth of the forming roll scanning – ultrasonic ”TR” method.
- Forming roll scanning ultrasonic method with a single element probe.
The System comprises the intuitive interface of its software, and uses the real drawing of the tested forming roll, as shown in Figure 4. The possibility of fast and easy adjustment and calibration is also envisaged. The Scanner’s movements are reflected in the coordinates system of B-35 in online mode.
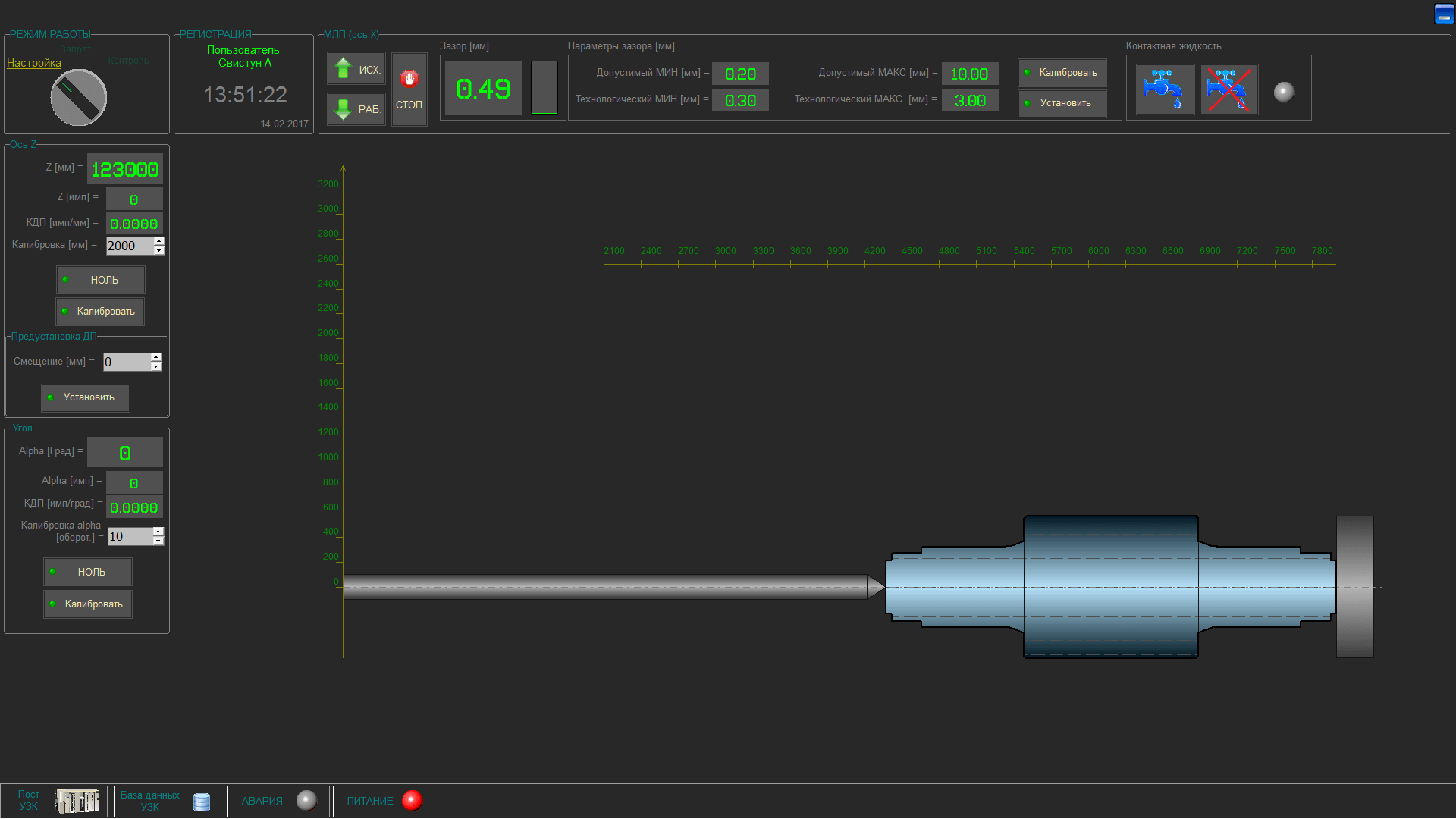
The operator has a possibility to review and to edit the DGS-diagrams which are plotted as a result of a roll body calibration.
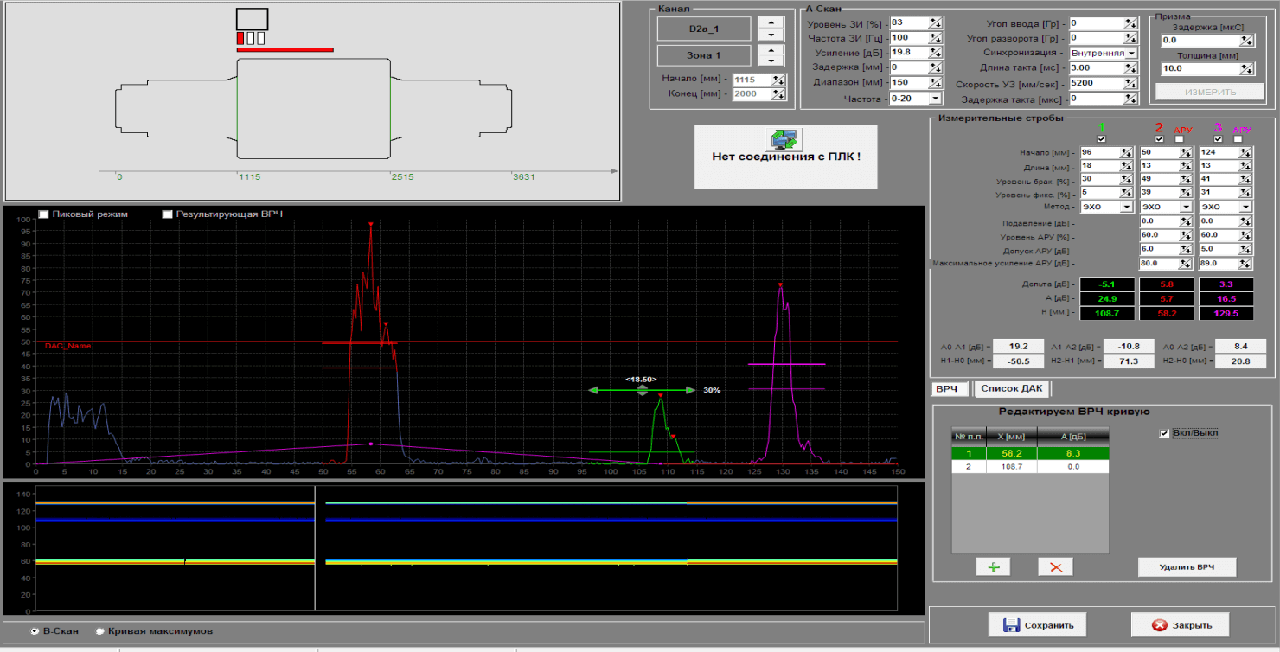
While performing a forming roll test, the operator can select the required regulatory documents and the rejection criteria, as well as one can select the calibration mode – either automatic, or to use the basic settings.
In the process of inspection, the minimization of uncontrolled zones at the start point and at the end of a forming roll is assured. Moreover, automatic correction of the Scanner’s position relative to the forming roll in 3-D space is provided (Figure 6).
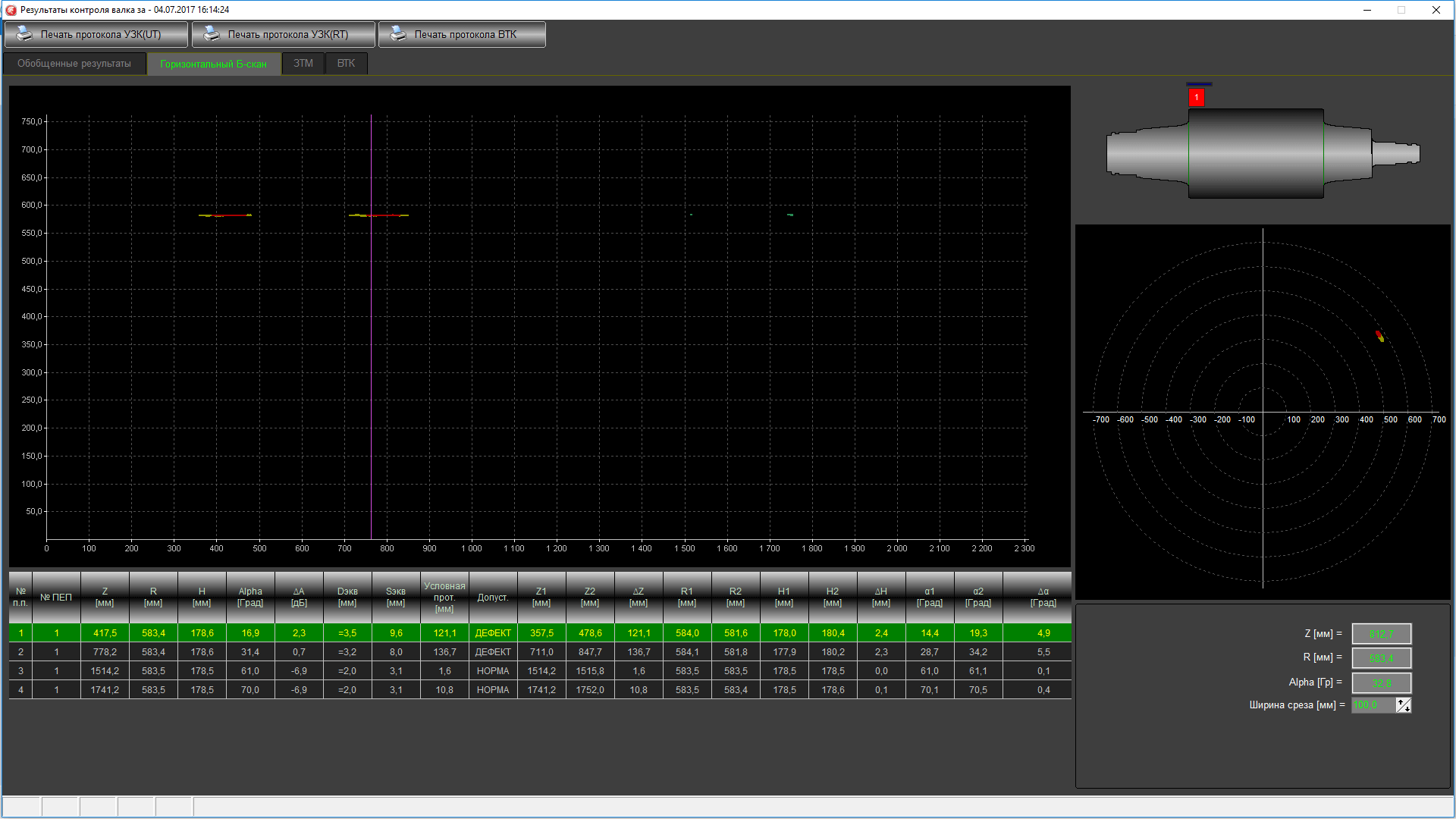
System software allows to review the results of inspection in 2-D mode for each test method (Fig. 7) and in 3-D mode for the mill roll in general (Fig.8). The System has also a feature to automatically generate the reports for each test method (Fig.9).
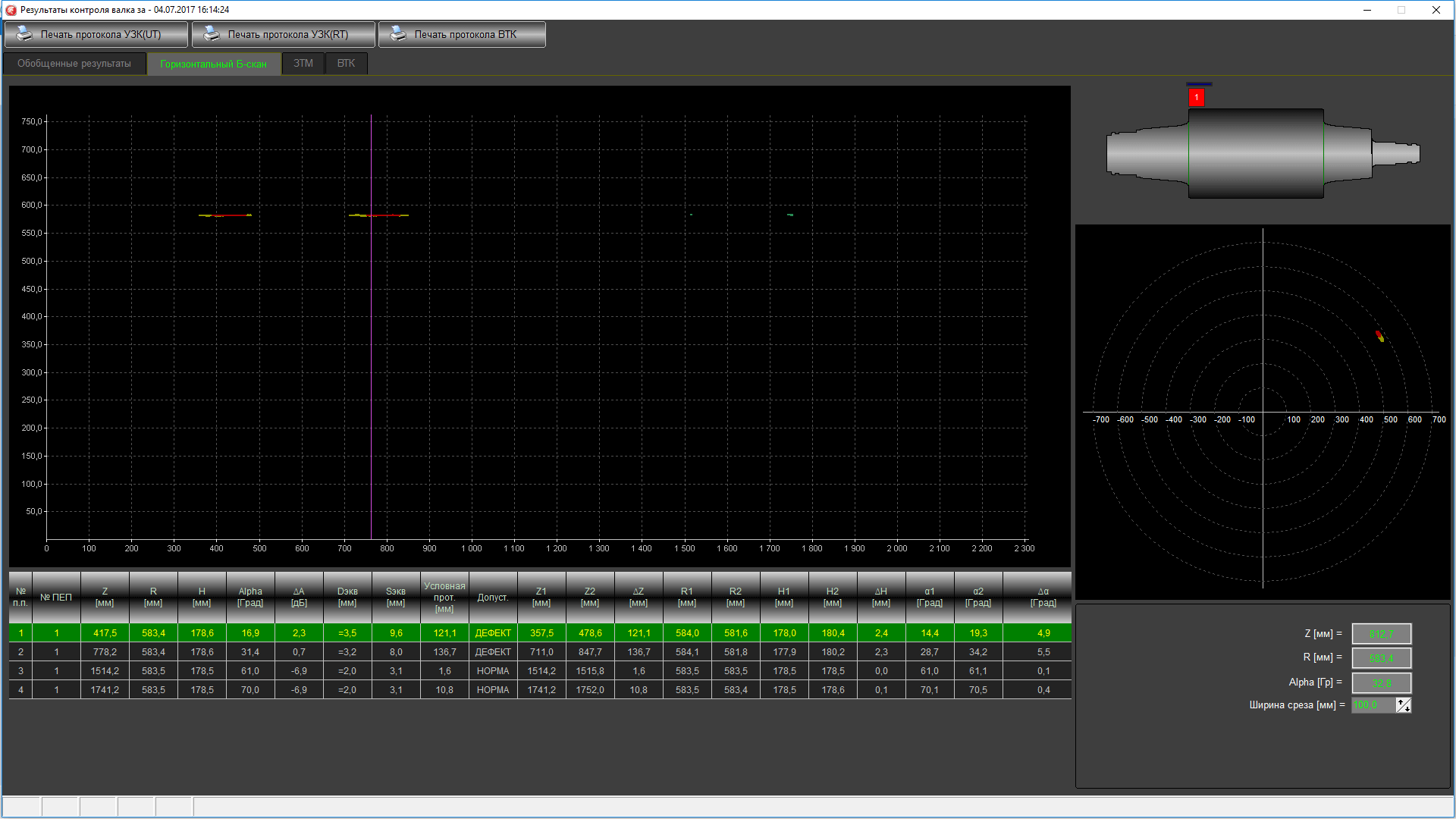
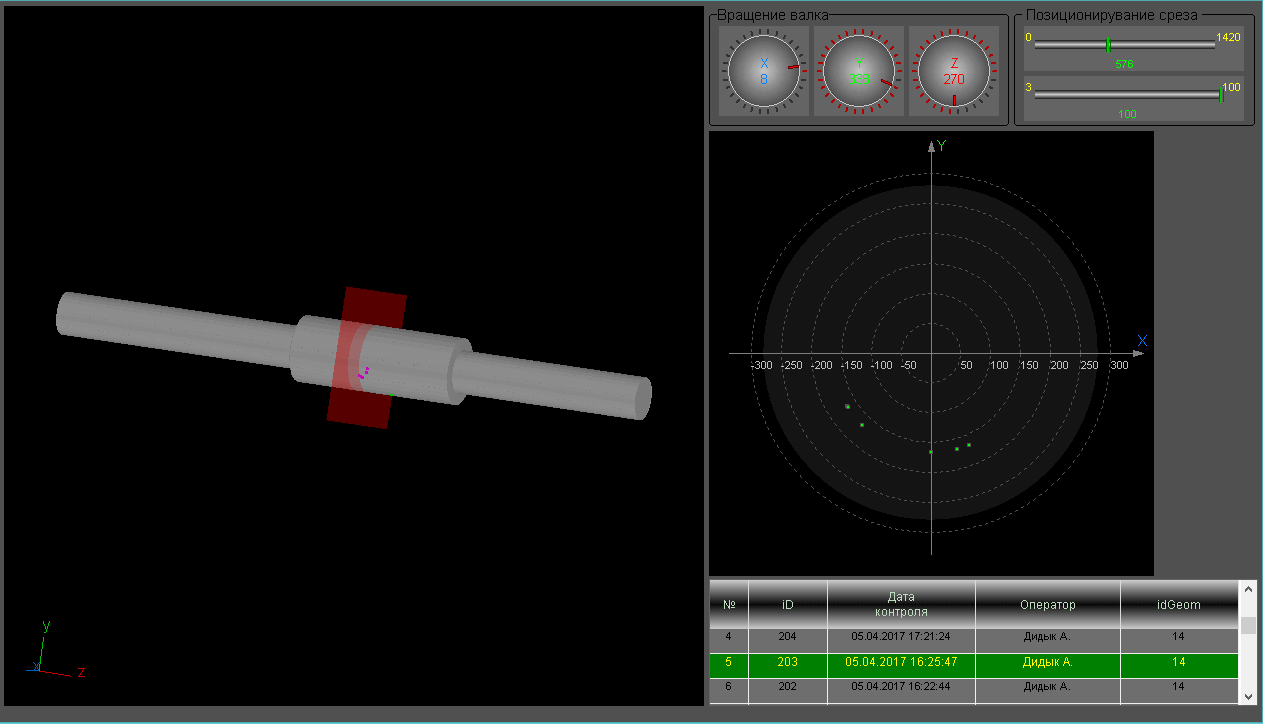
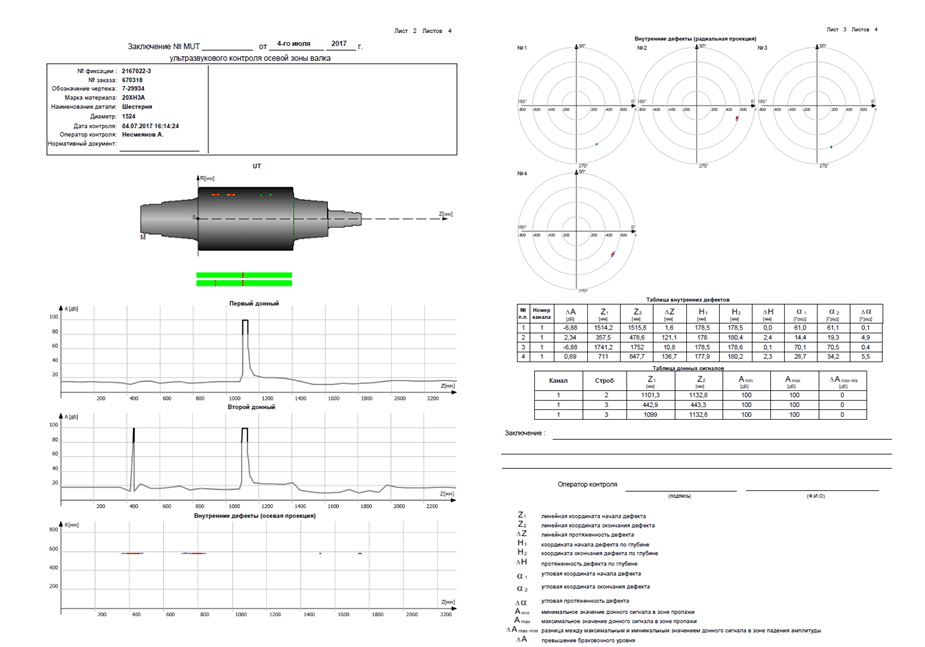
Application of the complex non-destructive testing System B-35 will allow to automatically record and evaluate internal and surface defects of the roll body, and to decide which production operations shall be performed further. Besides, specifications and NDT standards requirements as well as the customer’s requirements will be met in the same time.